What Are Vacuum Form Plastic Sheets and How Are They Used?
What Are Vacuum Form Plastic Sheets and How Are They Used?
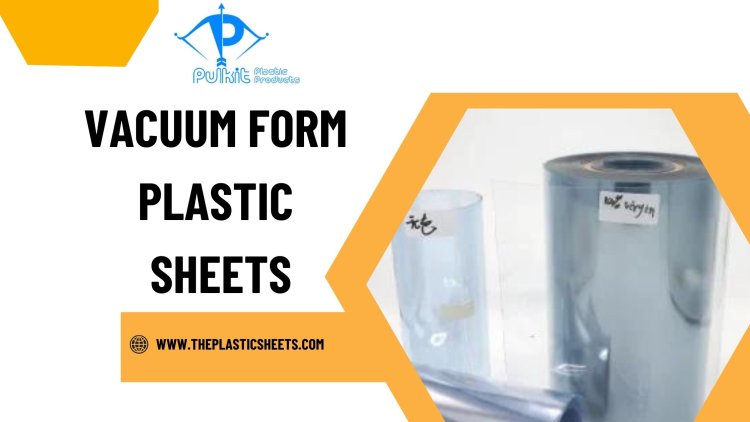
In the world of manufacturing, packaging, and product design, vacuum forming plastic sheets have become an essential material for a wide range of applications. Vacuum forming is a process that involves heating a plastic sheet until it is pliable, and then using a vacuum to mold it into a specific shape. This versatile method allows for the creation of intricate, detailed, and custom-shaped items, making it an essential tool in industries such as packaging, automotive, medical, and consumer goods. But what exactly are vacuum forming sheets, and how are they used in different industries?
In this article, we will explore what vacuum forming sheets are, how they are produced, their wide-ranging applications, and why they are an excellent choice for various manufacturing processes. Additionally, we will delve into the role of plastic sheet for vacuum forming and highlight a reputable vacuum forming sheet manufacturer, Pulkit Plastic Products, which provides high-quality products for diverse industrial needs.
What Are Vacuum Form Plastic Sheets?
A vacuum forming sheet is a type of plastic sheet used in the vacuum forming process. The material is typically made from a variety of thermoplastic materials that can be heated and molded into a specific shape under vacuum pressure. The plastic sheet is heated until it reaches a flexible, pliable state and then placed over a mold. A vacuum is applied, pulling the plastic tightly over the mold to take its shape. Once cooled, the plastic sheet solidifies into the desired form.
Common materials used for vacuum forming sheets include:
- Acrylic (PMMA): Known for its clarity and ability to be easily molded, acrylic is used in applications requiring transparency.
- Polyvinyl Chloride (PVC): A versatile plastic that is durable and resistant to chemicals, making it ideal for packaging and industrial uses.
- Polyethylene (PE): Lightweight and cost-effective, often used for food packaging or disposable containers.
- Polypropylene (PP): Known for its toughness, resistance to fatigue, and chemical resistance, used in automotive and medical applications.
- Polystyrene (PS): Often used for packaging, toys, and disposable cups due to its rigid nature and ease of forming.
How Vacuum Form Plastic Sheets Are Produced
The production of Vacuum forming plastic sheets involves several steps. The process begins with the selection of the appropriate material based on the end-use requirements, such as strength, clarity, or resistance to heat. Once the material is chosen, it is manufactured into large plastic sheets, which are then processed using a vacuum forming machine.
Here’s an overview of the typical vacuum forming process:
-
Heating: The plastic sheet is heated in an oven until it becomes soft and pliable. The sheet must be heated to the correct temperature for the material being used. For example, acrylic sheets may require a higher temperature than PVC sheets.
-
Forming: Once the plastic sheet is soft enough, it is placed over a mold. The mold can be made of various materials such as aluminum, steel, or wood, depending on the application. The mold is often designed with intricate details to shape the plastic precisely.
-
Vacuum Application: After the plastic sheet is positioned over the mold, a vacuum is applied. The vacuum pulls the plastic tightly over the mold, ensuring that it forms every detail. The suction force is strong enough to press the heated plastic into the contours of the mold, capturing the desired shape.
-
Cooling: Once the plastic has taken the shape of the mold, it is allowed to cool and solidify. This step ensures that the plastic retains its new form and maintains the required strength.
-
Trimming and Finishing: After cooling, the plastic sheet is removed from the mold and any excess material is trimmed away. Additional finishing processes such as drilling, painting, or printing can be applied depending on the final product requirements.
Applications of Vacuum Form Plastic Sheets
Vacuum formed plastic sheets are used in a wide variety of industries due to their versatility, strength, and cost-effectiveness. Here are some common applications:
1. Packaging
One of the most common uses of Vacuum sheet for packing is in the packaging industry. Vacuum-formed plastic sheets are often used to create blister packs, clamshell packaging, and other protective packaging products. This type of packaging is ideal for consumer goods like electronics, toys, pharmaceuticals, and food products. The clear, molded design not only offers protection but also enhances product visibility and presentation.
2. Automotive Parts
In the automotive industry, vacuum formed plastic sheets are used to produce parts such as dashboards, panels, and interior trim components. These parts require precise molding to fit into the vehicle's structure. Vacuum forming allows for the production of lightweight, durable, and cost-effective components that meet the high standards of the automotive industry.
3. Medical Equipment
The medical industry also makes use of vacuum-formed plastic sheets for items like medical trays, disposable containers, and protective covers. These items need to meet strict hygiene standards and be made from materials that are safe and resistant to chemicals. Vacuum forming is ideal for producing high-quality, precision-made medical products.
4. Point-of-Sale Displays
Retail businesses often use vacuum-formed plastic for creating custom point-of-sale displays. These displays can be molded into creative shapes, sizes, and designs to attract customer attention and showcase products. The lightweight nature of vacuum-formed plastic makes it easy to transport and set up in stores.
5. Consumer Goods
Vacuum-formed plastic sheets are also used in the production of consumer goods, such as food containers, trays, and storage solutions. The ability to create molded shapes with fine details makes these sheets suitable for producing items in a range of industries, including foodservice, home goods, and even toys.
6. Signage and Displays
Vacuum-formed plastic is frequently used for creating signage, lettering, and displays. The material's ability to hold vibrant colors and withstand outdoor conditions makes it an excellent choice for outdoor and indoor advertising. Signs, especially 3D signs, can be efficiently produced with vacuum forming techniques.
Benefits of Vacuum Form Plastic Sheets
-
Cost-Effective: Vacuum forming is a low-cost method for producing large quantities of custom-shaped plastic products. The materials are affordable, and the process requires fewer tools and molds than other manufacturing methods like injection molding.
-
Customizable: Vacuum forming allows for intricate shapes and designs, making it highly customizable for specific applications. Different material thicknesses and finishes can also be applied to achieve the desired aesthetic or functional qualities.
-
Lightweight: The finished plastic products are generally lightweight, which reduces shipping costs and makes them easier to handle.
-
Durable: Vacuum-formed plastics are strong, impact-resistant, and durable, which is why they are used in everything from automotive parts to packaging.
-
Versatile: Vacuum formed plastic sheets can be used in a wide range of industries and applications, making them a versatile solution for manufacturers.
Pulkit Plastic Products: A Trusted Supplier of Vacuum Forming Sheets
For businesses looking for high-quality vacuum forming sheets, Pulkit Plastic Products is a leading manufacturer and supplier. Pulkit Plastic Products provides a wide range of plastic sheets for vacuum forming, made from durable, reliable materials that meet the specific needs of different industries. Whether you're in the packaging industry, automotive sector, or any other field that requires custom-molded plastic products, Pulkit Plastic Products offers superior solutions that ensure quality, precision, and performance.
Their expertise in providing durable and versatile vacuum forming sheets has made them a trusted name in the industry. Pulkit Plastic Products focuses on customer satisfaction, offering tailored solutions for businesses that need high-quality vacuum forming sheets at competitive prices.
Conclusion
Vacuum forming plastic sheets are a highly versatile and cost-effective solution for creating custom plastic products across a variety of industries. From packaging to automotive and medical applications, vacuum-formed plastics play a crucial role in the design and manufacturing of consumer goods, parts, and displays. With the help of a reliable manufacturer such as Pulkit Plastic Products, businesses can access high-quality Plastic sheets for vacuum forming that meet their specific needs and ensure excellent results in the production process.
FAQ
1. What is a vacuum forming sheet?
A vacuum forming sheet is a type of plastic sheet used in the vacuum forming process. It is heated and then molded over a shape using vacuum pressure to create custom, detailed plastic products.
2. What types of plastic are used for vacuum forming?
Common plastics used for vacuum forming include acrylic, PVC, polyethylene, polypropylene, and polystyrene, depending on the application and required properties.
What's Your Reaction?
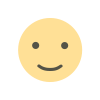
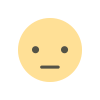
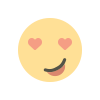
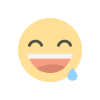
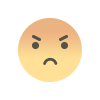
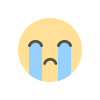
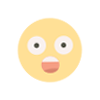