WeldSaver™ 6: Revolutionizing Welding Cooling Systems
WeldSaver™ 6 optimizes welding cooling with real-time flow monitoring, leak detection, and automated coolant control for enhanced efficiency.

In the world of welding, the importance of an efficient cooling system cannot be overstated. High temperatures during welding can lead to serious issues, including equipment damage, poor weld quality, and prolonged cooling times. For years, various cooling solutions have been employed, but with the introduction of the WeldSaver™ 6, there has been a revolutionary shift in how welding cooling systems are designed and implemented.
The WeldSaver™ 6 is a state-of-the-art solution developed to improve the efficiency of cooling systems in welding processes. It is a part of the Proteus Industries lineup and is known for its commitment to creating high-performance, reliable, and long-lasting products. The weld saver is designed to address the everyday challenges faced by enterprises that rely on welding processes, providing an advanced solution that optimizes cooling, improves operational efficiency, and extends the lifespan of the equipment.
How WeldSaver™ 6 Enhances Cooling Efficiency in Welding Systems
Cooling is a critical element in the welding process, as the heat caused during welding needs to be quickly dissipated to prevent overheating, warping, and equipment failure. Traditional cooling systems often struggle with maintaining consistent flow rates, leading to overheating of components, increased downtime, and inefficient energy use.
WeldSaver™ 6 addresses these issues by incorporating advanced technologies that optimize the flow of coolant within the system. It uses a highly accurate temperature control mechanism to regulate coolant flow, ensuring that the temperature of the welding components remains stable throughout the process. By preventing overheating and reducing thermal cycling, the WeldSaver™ 6 helps to maintain the integrity of the welds and the welding equipment.
One of the standout features of WeldSaver™ 6 is its ability to provide precise control over the cooling process. Unlike traditional cooling systems, which may rely on simple, unregulated flow, the WeldSaver™ 6 dynamically adjusts coolant flow based on real-time temperature measurements. This allows the system to cool components more efficiently, reducing energy consumption and increasing the overall performance of the welding process.
Moreover, by minimizing thermal stress and preventing overcooling, the WeldSaver™ 6 improves the longevity of the welding equipment, as it reduces the risk of damage to critical components like nozzles, tips, and electrodes.
The Key Features of WeldSaver™ 6 and Its Benefits
The WeldSaver™ 6 stands out in the welding industry due to its combination of cutting-edge features and tangible benefits. Let's take a closer look at some of the key features of the WeldSaver™ 6 and how they contribute to enhanced performance.
Adaptive Flow Control
One of the primary advantages of the WeldSaver™ 6 is its adaptive flow control technology. This feature ensures that the coolant flow rate is adjusted dynamically based on the temperature of the welding system. The ability to control the coolant flow in real time ensures optimal cooling without wasting energy. The adaptive flow control system is perfect for industries that deal with varying welding conditions, as it allows the system to adapt to changing heat loads, improving both the efficiency and effectiveness of the cooling process.
Robust and Durable Design
The WeldSaver™ 6 is designed to withstand the harshest conditions. Built with high-quality materials, it is engineered to last in demanding environments. The robust design not only ensures durability but also helps reduce care costs over the long term. Welding systems that are exposed to extreme heat, pressure, and pulse benefit significantly from the resilience of the WeldSaver™ 6, as it minimizes the need for repairs and replacement.
Compact and Easy Installation
The WeldSaver™ 6 is designed with space efficiency in mind. Its packed size causes it easy to incorporate into existing welding systems without the need for significant modifications. This feature is particularly valuable for industries looking to upgrade their cooling systems without a complete overhaul. Its straightforward installation process ensures minimal downtime, allowing businesses to continue operations with minimal interruption.
Energy Efficiency
Energy consumption is a vital concern for companies that rely on large-scale welding operations. The WeldSaver™ 6 offers energy-saving features that allow for precise control of the coolant flow, reducing the quantity of power needed to keep optimal temperatures. The energy-efficient design leads to cost savings over time, making it a valuable investment for businesses looking to reduce their operational costs.
Improved Safety Features
Safety is a top priority in any industrial operation, and the WeldSaver™ 6 incorporates several safety features to ensure the smooth functioning of the welding process. The system includes temperature sensors that monitor coolant flow in real-time, preventing overheating that could lead to accidents or equipment failure. These safety features help protect both the personnel and the equipment, ensuring that the welding process remains safe and efficient at all times.
Why WeldSaver™ 6 is the Future of Welding Cooling Technology
The WeldSaver™ 6 is a step forward in the evolution of welding cooling systems. As industries continue to push for greater efficiency, higher-quality welds, and lower operational costs, the WeldSaver™ 6 is emerging as the go-to solution for cooling needs in welding operations.
With its advanced temperature control, adaptive flow regulation, and energy-efficient design, the WeldSaver™ 6 addresses many of the shortcomings of traditional cooling systems. Its ability to optimize coolant flow ensures that welders can achieve consistent, high-quality welds without the risk of overheating or equipment failure.
Furthermore, the WeldSaver™ 6 is adaptable to a wide range of welding applications, from small-scale workshops to large industrial operations. Its versatility, combined with its energy-saving features, makes it a future-proof solution for industries looking to stay ahead of the competition.
Improved Weld Quality with WeldSaver™ 6 Cooling System
The quality of a weld is determined by many factors, with one of the most critical being temperature control. High temperatures during welding can lead to issues such as warping, cracking, and inconsistent welds. By maintaining an optimal temperature range, the WeldSaver™ 6 helps ensure that the weld pool remains stable, resulting in stronger, more consistent welds.
The system's ability to regulate the temperature of the welding components allows for precise heat management, which leads to better bead formation and stronger bonds between materials. Whether working with steel, aluminium, or other metals, the WeldSaver™ 6 ensures that each weld is performed at the ideal temperature for maximum strength and durability.
The Science Behind WeldSaver™ 6: Optimizing Temperature Control
At the heart of the WeldSaver™ 6 lies advanced temperature control technology. The system is designed to monitor the temperature of the welding components in real time and adjust the coolant flow accordingly. This precision allows for better control over the thermal properties of the weld, reducing the risks of thermal expansion, contraction, and material distortion.
The system's adaptive flow control works by constantly adjusting the coolant flow based on real-time temperature readings from various sensors within the welding system. This ensures that the temperature remains within an optimal range, preventing overheating or overcooling that could affect the quality of the weld.
Furthermore, the WeldSaver™ 6 uses advanced materials that improve heat dissipation, further enhancing the system's ability to maintain consistent temperatures throughout the welding process. The combination of precise flow control and advanced materials results in better temperature regulation, which is essential for high-quality welding operations.
Conclusion
The WeldSaver™ 6 is an essential tool for any welding operation seeking to improve the efficiency, safety, and quality of their work. Its adaptive flow control, durable design, energy efficiency, and low maintenance requirements make it a valuable investment for businesses in the welding industry.
As welding operations continue to evolve, the need for advanced, efficient cooling systems like the WeldSaver™ 6 will only grow. By providing optimal temperature control, enhancing weld quality, and reducing operational costs, the WeldSaver™ 6 is paving the way for the future of welding cooling technology.
FAQs
What is the main benefit of the WeldSaver™ 6?
The main benefit of the WeldSaver™ 6 is its ability to optimize coolant flow for efficient temperature regulation, leading to improved weld quality, reduced energy consumption, and longer equipment life.
Can the WeldSaver™ 6 be installed in existing systems?
Yes, the WeldSaver™ 6 is designed to be easily integrated into existing welding systems, making it a flexible and cost-effective solution for upgrades.
How does the WeldSaver™ 6 save energy?
The WeldSaver™ 6 uses adaptive flow control to regulate the coolant flow based on real-time temperature readings, reducing the amount of coolant used and preventing excess energy consumption.
What metals can the WeldSaver™ 6 be used with?
The WeldSaver™ 6 is versatile and can be used for welding various metals, including steel, aluminium, and more, by maintaining the ideal temperature for each material.
How often does the WeldSaver™ 6 require maintenance?
The WeldSaver™ 6 is designed to be low-maintenance, requiring only regular inspections to ensure optimal performance, minimizing downtime and repair costs.
What's Your Reaction?
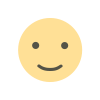
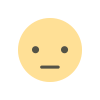
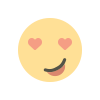
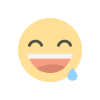
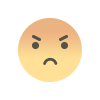
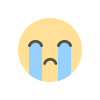
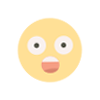