SolidWorks Sheet Metal Design: From Basics to Advanced Techniques
Sheet metal design in SolidWorks is essential for industries like automotive, aerospace, and manufacturing.

Sheet metal design in SolidWorks is essential for industries like automotive, aerospace, and manufacturing. Mastering these tools allows engineers to create accurate, manufacturable sheet metal parts efficiently. This guide covers key SolidWorks sheet metal techniques, from basic features to advanced workflows.
Enrolling in a SolidWorks Online Course can help professionals gain hands-on expertise in sheet metal modeling, bending, and unfolding techniques. A structured course provides in-depth training on design automation, simulation, and manufacturing best practices, making it easier to create precise and production-ready designs.
Fundamentals of Sheet Metal Design in SolidWorks
SolidWorks provides specialized tools to simplify the creation of sheet metal parts, allowing engineers to design precise, manufacturable components used in industries such as automotive, aerospace, and manufacturing. Understanding the fundamental operations of SolidWorks sheet metal design is crucial for creating durable and efficient parts. Below are some key operations used in sheet metal modeling:
1. Base Flange/Tab
-
The Base Flange/Tab is the foundation feature of a sheet metal part.
-
It is created by selecting a sketch profile, which is then extruded to form the base sheet metal body.
-
The thickness of the part is defined in this step, and it serves as the starting point for additional bends, flanges, and cuts.
2. Bend
-
The Bend tool is used to add bends to a flat sheet metal part, allowing it to take complex shapes while maintaining manufacturability.
-
Bend radii, angles, and k-factor values are critical to ensuring proper bend allowance and material stretching.
-
Using the Bend tool ensures the part follows manufacturing standards and can be easily fabricated.
3. Lofted Bends
-
The Lofted Bends feature helps in creating smooth transitions between different profiles, such as a rectangular-to-round duct.
-
This operation is particularly useful for HVAC ductwork, aerospace panels, and complex enclosures.
-
It allows engineers to design parts that would otherwise be difficult to manufacture using traditional bending techniques.
4. Edge Flange
-
The Edge Flange extends the edge of a sheet metal part, creating additional support or connection points.
-
Engineers can control parameters like angle, flange length, and bend radius to achieve the required shape.
-
This feature is widely used in bracket design, enclosures, and panel reinforcements.
5. Hem
-
The Hem tool folds the edge of the sheet metal to:
-
Eliminate sharp edges for safety.
-
Increase structural strength and prevent deformation.
-
Improve part aesthetics and reduce the risk of material cracking.
-
Hems come in various types, including open, closed, and rolled hems, depending on the design requirements.
Sheet Metal Features and Their Functions
Feature |
Purpose |
Usage |
Base Flange |
Creates the first sheet metal feature |
Initial design setup |
Edge Flange |
Extends an edge in any direction |
Strengthening sheet metal |
Lofted Bends |
Generates complex transitions between profiles |
Air ducts, hoods, enclosures |
Jog |
Creates an offset in a sheet metal part |
Avoiding material interference |
Hem |
Folds the edge to eliminate sharpness |
Safety and strength |
Advanced Techniques: Enhancing Sheet Metal Efficiency
1. Multi-Body Sheet Metal Design
-
Allows for creating multiple components in one part file.
-
Useful in assemblies where parts interact.
2. Sheet Metal Cost Estimation
-
SolidWorks can generate cost estimates based on material, size, and bends.
-
Helps in budgeting and cost optimization.
3. Design for Manufacturing (DFM) in Sheet Metal
-
Ensures sheet metal parts can be manufactured efficiently.
-
Checks for manufacturability errors before production.
Manual vs. SolidWorks Sheet Metal Design
SolidWorks Training in Noida: The Tech Industry Hub
Noida is home to major industrial and engineering firms, making it a great place for learning CAD software. A SolidWorks Course in Noida provides industry-oriented training, covering real-world applications in automotive, aerospace, and manufacturing companies.
For professionals looking for flexible learning options, enrolling in a SolidWorks Online Course is a great way to gain expertise in 3D modeling, sheet metal design, and simulation tools. Online courses offer hands-on training, allowing learners to master SolidWorks from anywhere while staying updated with industry trends.
Training in Delhi: A Center for Engineering Innovation
Delhi has a rapidly growing tech sector with various startups and large enterprises investing in CAD software. A SolidWorks Course in Delhi can help professionals get hands-on experience with industry-driven projects.
SolidWorks Trends in Delhi
-
Growing demand for CAD professionals in manufacturing.
-
Increased use of SolidWorks for 3D product visualization.
-
Expanding engineering design firms looking for trained experts.
SolidWorks Usage Across Industries
Conclusion
SolidWorks Sheet Metal tools offer powerful capabilities for designing, analyzing, and manufacturing sheet metal parts efficiently. Whether you are working in automotive, aerospace, or industrial manufacturing, mastering these tools can significantly enhance your design workflow and career prospects.
What's Your Reaction?
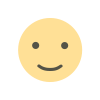
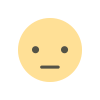
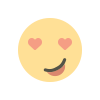
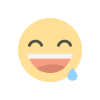
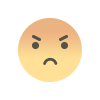
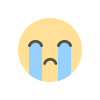
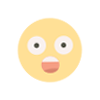