Gummy Manufacturing Process: How Quality Supplements Are Made
Discover the gummies manufacturing process from raw materials to finished products. See how premium nutraceutical gummies are produced.

Walk through the doors of a modern gummies manufacturing facility, and you'll find a fascinating blend of culinary artistry and pharmaceutical precision. The global gummy vitamin market, projected to reach $10.9 billion by 2027, relies on advanced manufacturing processes to deliver effective, great-tasting supplements.
At Your Gummy Vitamins (YGV), we've perfected the craft of nutraceutical gummy production through years of innovation. This exclusive behind-the-scenes tour reveals each step of transforming raw ingredients into shelf-ready private label gummies that consumers love.
Section 1: Raw Materials – The Foundation of Quality
Ingredient Sourcing & Inspection
Every batch begins with:
✔ Pharmaceutical-grade active ingredients (vitamins, minerals, botanicals)
✔ Natural sweeteners (organic cane sugar, tapioca syrup, or sugar alternatives)
✔ Gelatin or pectin bases (animal or plant-derived)
✔ Flavors & colors (fruit extracts preferred over artificial)
Quality Control Checkpoint:
All raw materials undergo:
-
Identity verification (HPLC testing)
-
Potency assays
-
Microbiological screening
-
Heavy metal testing
Section 2: The Manufacturing Process Step-by-Step
1. Premixing Station
-
Dry ingredients blended in controlled humidity rooms
-
Liquid ingredients pre-mixed separately
-
Temperature-sensitive actives set aside
2. Cooking & Melting
-
Precision stainless steel kettles heat mixtures to 70-85°C
-
Continuous stirring prevents hot spots
-
Cooking time strictly monitored (varies by formula)
3. Active Ingredient Incorporation
-
Heat-sensitive nutrients (like probiotics) added last
-
Specialized cooling jackets protect delicate compounds
-
Homogenization ensures even distribution
4. Depositing into Molds
-
Food-grade silicone molds move on conveyor belts
-
Computer-controlled depositors fill 5,000+ gummies/minute
-
Multiple shapes available (bears, rings, fruits)
5. Drying & Curing
-
24-48 hours in climate-controlled chambers
-
Humidity maintained at 30-40%
-
Regular texture checks ensure perfect chew
Section 3: Quality Control – Beyond Industry Standards
In-Process Testing
Checkpoint |
Method |
Standard |
Viscosity |
Brookfield Viscometer |
15,000-25,000 cP |
pH Level |
Digital pH Meter |
3.8-4.2 |
Brix (Sweetness) |
Refractometer |
72-78° Brix |
Finished Product Testing
-
Potency Verification (HPLC/GC)
-
Texture Analysis (TA.XT Plus Texture Analyzer)
-
Stability Testing (3/6/12 month studies)
-
Dissolution Testing (Nutrient release rates)
Section 4: Packaging – Where Science Meets Marketing
Popular Packaging Options
Type |
Best For |
MOQ |
Glass Apothecary Jars |
Premium brands |
5,000 units |
Child-Resistant Pouches |
Cannabis market |
10,000 units |
Blister Packs |
Sample sizes |
15,000 units |
Labeling Essentials
✔ FDA-compliant Supplement Facts panel
✔ Certified organic/non-GMO seals (when applicable)
✔ QR code linking to third-party test results
✔ Clear dosage instructions
Section 5: Emerging Technologies in Gummy Manufacturing
1. 3D Printing
-
Custom shapes for brand differentiation
-
Layer-by-layer nutrient incorporation
2. Hot Melt Extrusion
-
Better heat-sensitive nutrient retention
-
30% faster production times
3. Microencapsulation
-
Protects delicate ingredients (probiotics, enzymes)
-
Enables time-release formulations
4. Automated Visual Inspection
-
AI-powered cameras detect imperfections
-
99.9% defect-free guarantee
5 Customer Success Stories
⭐⭐⭐⭐⭐ "YGV's transparency about their gummies manufacturing process gave us complete confidence." – Nature's Balance
⭐⭐⭐⭐⭐ "The quality control is unmatched – our products always test at 100% potency." – VitaFusion
⭐⭐⭐⭐⭐ "Their small-batch capability let us test 3 formulas before scaling." – Herb & Root
⭐⭐⭐⭐⭐ "The pectin-based gummies exceeded our texture expectations." – GreenLife
⭐⭐⭐⭐⭐ "From concept to shelf in just 8 weeks – incredible turnaround." – NutraPure
5 Essential FAQs
1. How long does production take from start to finish?
Standard timelines:
-
2 weeks for samples
-
4-6 weeks for full production runs
2. What's the minimum order quantity?
Most manufacturers require:
-
5,000 units for standard orders
-
1,000 units for sample batches
3. Can you make allergen-free gummies?
Yes! We offer:
-
Top 8 allergen-free facilities
-
Vegan, gluten-free, and non-GMO options
4. How do you ensure consistent gummy texture?
Through:
-
Precise humidity control
-
Advanced drying protocols
-
Regular texture analyzer checks
5. What packaging is most cost-effective?
Stand-up pouches typically offer:
-
40% lower cost than glass jars
-
Higher shelf visibility
-
Smaller storage footprint
Conclusion: Why Manufacturing Expertise Matters
Choosing the right gummies manufacturing partner affects:
✔ Product efficacy – Proper nutrient preservation
✔ Brand reputation – Consistent quality builds trust
✔ Profit margins – Efficient processes reduce waste
At Your Gummy Vitamins, we combine:
-
Pharmaceutical-grade standards
-
Culinary creativity
-
Cutting-edge technology.
What's Your Reaction?
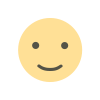
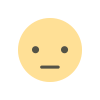
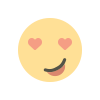
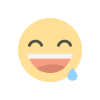
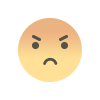
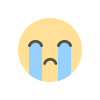
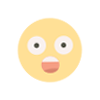