Enhancing Collaboration in Prefabricated Construction: Bridging Manufacturers and On-Site Teams
Discover strategies to enhance collaboration in prefabricated construction, bridging manufacturers and on-site teams for seamless project execution.

Prefabricated construction is transforming the building industry, offering efficiency, cost savings, and sustainability. However, seamless collaboration between prefabrication manufacturers and on-site teams is essential to maximize these benefits. Without proper communication and coordination, even the most well-planned projects can face costly delays and inefficiencies. Connective Consulting Group specializes in optimizing workflows between manufacturers and construction teams, ensuring smooth execution from production to installation.
To achieve success in modular construction, aligning supply chain logistics, ensuring real-time communication, and leveraging technology-driven solutions can bridge the gap between prefab factories and job sites. Let’s explore practical strategies to enhance collaboration for better project outcomes.
The Importance of Collaboration in Prefabricated Construction
Bridging the gap between off-site manufacturing and on-site assembly is crucial for avoiding delays and ensuring project success. Effective collaboration results in:
-
Improved project efficiency – reducing construction time and on-site labor costs.
-
Enhanced quality control – ensuring prefabricated components meet specifications.
-
Minimized waste – optimizing material usage and reducing rework.
-
Streamlined logistics – ensuring just-in-time delivery and storage solutions.
Key Challenges in Prefabricated Construction Collaboration
Despite its benefits, prefab construction faces hurdles that can disrupt project timelines and budgets. The major challenges include:
-
Communication Gaps – Misalignment between manufacturers and on-site teams can lead to errors and project delays.
-
Design Integration Issues – Prefab elements must fit seamlessly with on-site structures, requiring detailed planning.
-
Logistics and Scheduling Conflicts – Coordinating deliveries with installation timelines is critical to avoid bottlenecks.
-
Limited Flexibility – Prefabrication requires early decision-making, leaving little room for last-minute changes.
Best Practices for Enhancing Collaboration
To bridge the divide between manufacturers and construction teams, consider implementing the following strategies:
1. Leverage Technology for Seamless Communication
Utilizing Building Information Modeling (BIM) and cloud-based project management tools can facilitate real-time collaboration. BIM allows for digital modeling, reducing design conflicts, while platforms like Procore, Autodesk Construction Cloud, and PlanGrid improve information flow across all teams.
2. Establish Clear Roles and Responsibilities
A well-defined collaboration framework ensures all stakeholders understand their roles, reducing confusion and enhancing accountability. Conducting pre-construction meetings can align expectations between manufacturers, designers, and contractors.
3. Implement a Just-in-Time Delivery System
To avoid on-site congestion and storage issues, synchronize prefabricated component deliveries with installation schedules. Working closely with logistics providers and setting up real-time tracking can improve coordination.
4. Standardize Components for Greater Flexibility
Using standardized prefabricated elements enhances interchangeability, making on-site assembly more adaptable. This reduces the risk of delays caused by custom modifications or mismatched parts.
5. Foster Strong Manufacturer-Contractor Relationships
Creating long-term partnerships between prefabrication manufacturers and contractors builds trust and improves efficiency. Regular site visits, open communication channels, and collaborative problem-solving can strengthen these relationships.
6. Train On-Site Teams in Prefabricated Construction Techniques
Since prefab construction differs from traditional methods, training programs ensure on-site crews understand installation processes, reducing errors and rework. Investing in workshops, webinars, and hands-on training improves efficiency.
7. Conduct Regular Site and Factory Inspections
Regular quality checks and inspections help ensure that prefabricated components meet specifications before they arrive on-site. Factory inspections allow for corrections before production is complete, preventing costly rework at the construction site.
8. Utilize Digital Twins for Better Coordination
A digital twin is a virtual replica of the project that allows teams to visualize the assembly process in real time. By using digital twin technology, manufacturers and contractors can identify potential issues before they become costly problems.
9. Adopt Lean Construction Principles
Lean construction methods focus on reducing waste and improving workflow efficiency. Prefabrication benefits greatly from lean principles, as they help optimize scheduling, reduce resource wastage, and ensure smooth project execution.
10. Encourage Early Collaboration in Design
Bringing manufacturers, architects, and contractors together during the design phase helps avoid clashes between prefab components and on-site structures. Early collaboration ensures that prefabrication elements are properly integrated into the overall project plan.
Case Study: Successful Collaboration in Action
Consider a high-rise modular housing project in New York City, where manufacturers and on-site teams worked seamlessly. By leveraging BIM technology, real-time tracking, and pre-planned deliveries, the project:
-
Reduced construction time by 30%
-
Cut material waste by 25%
-
Achieved a 95% defect-free installation rate
Another example is a hospital expansion project in California, where the use of prefabricated wall panels and modular mechanical systems streamlined construction. By incorporating early-stage planning, manufacturer input, and just-in-time delivery, the project was completed ahead of schedule and under budget.
Such success stories highlight the importance of proactive collaboration in prefab construction.
Future Trends in Prefabricated Construction Collaboration
The construction industry continues to evolve, with emerging trends further enhancing collaboration:
-
AI and Machine Learning Integration – Predictive analytics can optimize supply chain management and construction sequencing.
-
Blockchain for Construction Contracts – Smart contracts improve transparency and ensure compliance between stakeholders.
-
Augmented Reality (AR) for Site Coordination – AR technology allows teams to visualize prefab components on-site before installation.
-
Sustainability-Driven Collaboration – Prefabrication manufacturers are adopting greener materials and energy-efficient processes to meet sustainability goals.
Conclusion
Enhancing collaboration between prefabrication manufacturers and on-site teams is essential for optimizing modular construction projects. By leveraging technology, clear communication, and strategic planning, teams can reduce delays, improve quality, and maximize efficiency.
As prefabricated construction continues to rise in popularity, fostering strong manufacturer-contractor relationships, embracing digital solutions, and adopting lean methodologies will be key to success.
How do you ensure smooth collaboration in your prefab projects? Share your experiences and insights in the comments!
What's Your Reaction?
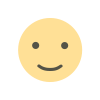
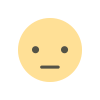
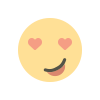
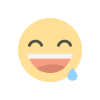
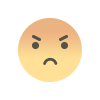
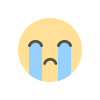
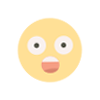