Always Ready: How HACCP Enhances Audit Preparedness in Indian Biopharma
Learn how HACCP helps Indian biopharma companies stay audit-ready, improving compliance and supporting Make in India and Atmanirbhar Bharat goals.
Always Ready: How HACCP Enhances Audit Preparedness in Indian Biopharma
In biopharmaceutical manufacturing, excellence is not just demonstrated in products—it must be proven on paper and during inspections. In an industry where regulatory scrutiny is high and trust is everything, audit preparedness isn’t an option; it’s a necessity.
For Indian companies aiming to lead in global healthcare, this level of preparedness is built on Hazard Analysis and Critical Control Points (HACCP)—a proactive safety system that supports every facet of compliance, from production floors to documentation offices. As India aligns its industrial strategies with the visions of Make in India and Atmanirbhar Bharat, implementing HACCP systems not only enhances safety and quality—it also ensures that companies are always inspection-ready, whether for domestic regulatory audits or global certifications.
This blog explores how HACCP strengthens audit readiness in Indian biopharma, supports regulatory excellence, and ultimately contributes to India’s emergence as a global biopharmaceutical leader.
The High-Stakes World of Biopharma Audits
Biopharmaceuticals differ from standard chemical drugs due to their complexity and sensitivity. Whether it's a monoclonal antibody, a recombinant vaccine, or a cell therapy product, the risks involved are significant. Hence, regulators across the world conduct frequent and detailed audits to ensure that these products are manufactured safely.
Some common audit types include:
-
Internal audits by the company’s quality team
-
Regulatory audits from CDSCO, USFDA, EMA, or WHO
-
Customer audits by overseas buyers
-
Certification audits for GMP, ISO, or WHO prequalification
Each of these audits focuses on process control, documentation integrity, staff training, corrective actions, and facility hygiene. Companies that fail audits risk product recalls, license suspensions, or export bans.
This is where HACCP-based systems become game changers—because they make compliance a daily habit, not a last-minute rush.
How HACCP Supports Audit Preparedness
The HACCP framework, rooted in prevention, transparency, and traceability, aligns perfectly with what auditors look for. By systematically identifying hazards, establishing critical control points (CCPs), and monitoring operations continuously, companies create an ecosystem where audit-readiness is embedded into operations.
Key areas where HACCP enhances audit success:
-
Proactive documentation that reflects real-time process control
-
Defined roles and responsibilities across departments
-
Evidence-based corrective actions for every deviation
-
Ongoing verification and validation of safety systems
-
Training logs and competency assessments for staff
When implemented correctly, HACCP systems provide auditors with a clear, coherent narrative of quality, reducing surprises and improving inspection outcomes.
Documentation: The Auditor’s Lens
One of the pillars of both HACCP and audits is comprehensive documentation. For every hazard assessed, every control implemented, and every deviation managed, there must be a record.
Auditors typically review:
-
HACCP plans and flowcharts
-
CCP monitoring logs
-
Deviation reports and CAPA (Corrective and Preventive Action) summaries
-
Calibration records of instruments used in monitoring
-
Staff training logs and SOP acknowledgments
In this field study, the most audit-ready Indian biopharma firms were those that had not only implemented HACCP but had also integrated it deeply with their document control systems.
Digitized documentation is increasingly preferred, as it:
-
Ensures real-time data capture
-
Minimizes the risk of data loss
-
Provides easy retrieval during audits
-
Enhances traceability across multiple locations
Verification: A Core Principle for Continuous Compliance
Verification is the sixth principle of HACCP and perhaps the most relevant for audits. It requires companies to routinely test and confirm that their HACCP systems are working effectively.
Verification activities include:
-
Internal audits
-
Product testing
-
Environmental monitoring
-
Process revalidation
-
Review of CCP deviations and corrective actions
Auditors closely inspect how companies use verification findings to improve systems. Organizations that regularly verify and update their HACCP plans often score higher during inspections and receive fewer observations.
Building a Culture of Inspection Readiness
Audit preparedness is not a one-time task. It must be part of a company’s culture. HACCP enables this cultural shift by making risk awareness and control everyone’s responsibility—from senior management to production operators.
Here’s how HACCP drives this mindset:
-
Staff know their roles in maintaining CCPs and responding to deviations
-
Supervisors are trained to interpret HACCP data and trigger actions
-
Quality teams regularly review documentation for gaps or errors
-
Management reviews the HACCP system to ensure its continued relevance
This approach ensures that audit readiness is not left to the quality department alone—it becomes an organizational standard.
Training for Audit Preparedness via HACCP
A significant portion of audit observations stem from staff-related issues—poor record-keeping, lack of awareness, or procedural shortcuts. HACCP requires companies to train and assess employees regularly, making them confident participants in compliance.
Training modules often include:
-
Understanding hazards and CCPs
-
Proper documentation techniques
-
How to respond to deviations
-
Role-based expectations during audits
-
Mock audit sessions
This training prepares employees not just for doing their jobs, but also for answering auditor questions accurately and confidently—a key differentiator in successful inspections.
HACCP and Regulatory Alignment in India
The Central Drugs Standard Control Organization (CDSCO), India’s main regulatory body for pharma, has begun recognizing HACCP as part of its modernized approach to risk-based inspections. Companies that follow HACCP practices often find it easier to:
-
Align with Good Manufacturing Practices (GMP)
-
Handle regulatory audits with fewer observations
-
Prepare for overseas inspections with minimal changes
Moreover, HACCP principles are embedded in global audit guidelines from:
-
WHO
-
USFDA
-
EMA
-
PIC/S
This alignment helps Indian companies scale faster into international markets, fulfilling both Make in India’s export objectives and Atmanirbhar Bharat’s vision of self-sufficiency.
Digital Tools That Support HACCP-Based Audit Readiness
India’s move toward Digital India has influenced the pharmaceutical sector as well. Companies are now integrating digital systems that support HACCP monitoring and documentation.
Popular tools include:
-
CCP monitoring software with real-time dashboards
-
Audit readiness platforms with checklists and logs
-
Document control systems that auto-update SOP versions
-
Training management systems that track certifications and gaps
These tools reduce human error, improve traceability, and help companies present clean, complete, and compliant records during audits.
Atmanirbhar Bharat and Audit Independence
One of the goals of Atmanirbhar Bharat is not just to make more in India—but to own the systems that ensure those products are of global standard. A strong HACCP system empowers Indian companies to:
-
Reduce dependence on foreign consultants for audit preparation
-
Develop in-house teams trained in international audit expectations
-
Automate compliance without sacrificing operational control
This self-reliance in compliance builds reputational strength and operational independence, which is critical in competitive global pharmaceutical supply chains.
The Role of Internal Audits in Strengthening External Performance
Routine internal HACCP audits help companies preemptively identify gaps and correct them before regulators do. These audits mirror external inspections and serve as a compliance rehearsal.
Benefits include:
-
Identifying documentation gaps early
-
Reinforcing SOP adherence
-
Re-training staff based on audit findings
-
Demonstrating a proactive compliance culture
A company that audits itself regularly is more likely to pass external audits with minimal findings, building credibility with regulators and customers alike.
Common Audit Pitfalls Avoided Through HACCP
1. Unverified CCPs
Auditors often flag missing evidence that CCPs are actively monitored and validated. HACCP addresses this by requiring ongoing checks and supporting data.
2. Inconsistent Records
SOPs and monitoring logs that don’t match are a red flag. With HACCP, all documentation flows from a central system and supports each other.
3. Untrained Staff
Auditors will question employees. HACCP’s built-in training requirement ensures that everyone knows their role and can answer confidently.
4. No Corrective Action History
A spotless record can actually raise suspicion. HACCP ensures that all deviations are logged, investigated, and corrected with proof.
By embedding HACCP, Indian companies avoid these pitfalls and turn audits into opportunities to showcase excellence.
Conclusion: Confidence Through Control
In India’s rapidly evolving biopharmaceutical landscape, being ready for audits is no longer about scrambling to prepare documents or coaching staff at the last minute. With a well-implemented HACCP system, audit preparedness becomes part of everyday operations.
By fostering a culture of documentation, verification, training, and real-time monitoring, HACCP empowers Indian companies to face any audit with confidence. More importantly, it aligns with the country’s larger ambitions—to manufacture locally, comply globally, and lead internationally.
As Make in India builds capacity and Atmanirbhar Bharat promotes self-reliance, audit-ready HACCP systems ensure that every product leaving an Indian biopharma plant is not just effective—but proven safe, reliable, and compliant.
???? Bibliography
Dhiman, K., & Dadwal, N. (2025). Implementation of hazard analysis and critical control points (HACCP) in Indian biopharmaceutical industries: A field study. Environment Conservation Journal, 26(1), 84–90. https://doi.org/10.36953/ECJ.28512885
What's Your Reaction?
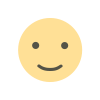
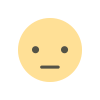
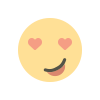
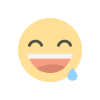
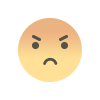
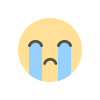
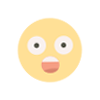