10 Tips For Crafting The Perfect Metal Punch And Die Set
In this comprehensive guide, we'll explore ten expert tips to help you optimize a metal punch and die set, from selecting the right materials to fine-tuning your techniques for maximum efficiency and precision.
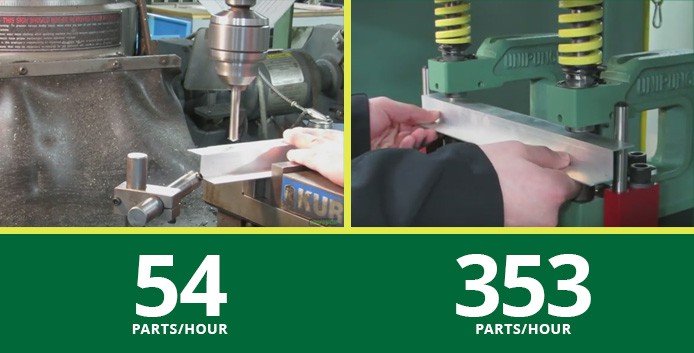
Metal punch and die sets are essential tools in manufacturing and fabrication processes, allowing for precise shaping and cutting of metal components. Whether you're working with sheet metal, aluminum, or stainless steel, mastering the art of crafting the perfect punch and die setup is crucial for achieving high-quality results. In this comprehensive guide, we'll explore ten expert tips to help you optimize a metal punch and die set, from selecting the right materials to fine-tuning your techniques for maximum efficiency and precision.
Understand Your Material
Before diving into crafting a metal punch and die set, it's essential to understand the properties of the material you'll be working with. Different metals have varying strengths, densities, and malleability, which can impact the design and performance of your punch and die set. Conduct thorough research or consult with materials experts to determine the best approach for punching and shaping your specific metal alloy.
Choose the Right Tool Steel
Selecting the right tool steel for your punch and die set is critical for achieving optimal performance and longevity. Look for high-quality tool steels with excellent wear resistance, toughness, and hardness properties to withstand the rigors of metalworking operations. Common tool steel grades used in punch and die manufacturing include A2, D2, S7, and M2, each offering unique advantages for specific applications.
Optimize Punch and Die Design
The design of your punch and die components plays a significant role in the success of your metalworking operations. Optimize the geometry, clearance, and relief angles of your punches and dies to ensure clean, precise cuts and minimize tool wear. Consider factors such as material thickness, hole size, and surface finish requirements when designing your punch and die profiles to achieve the desired results.
Maintain Proper Clearances
Maintaining proper clearances between the punch and die is essential for achieving consistent and accurate results in metal punching operations. Insufficient clearance can lead to burrs, deformation, and tool breakage, while excessive clearance may result in poor-quality cuts and dimensional inaccuracies. Follow manufacturer recommendations or industry standards to determine the appropriate clearance values for your specific punch and die setup.
Lubricate for Smooth Operation
Applying lubrication to your metal punch and die components is crucial for ensuring smooth operation and extending tool life. Proper lubrication reduces friction, heat buildup, and wear between the punch and die surfaces, resulting in cleaner cuts and reduced tool maintenance requirements. Choose lubricants specifically formulated for metalworking applications and apply them regularly to prevent galling, seizing, or adhesive wear during punching operations.
Implement Proper Die Clearance
Maintaining the correct die clearance is essential for achieving precise and consistent results in metal punching processes. Die clearance refers to the gap between the punch and die cavity, allowing for material deformation and shearing during the punching operation. Adjust the die clearance based on the material type, thickness, and punch diameter to optimize cutting performance and minimize tool wear.
Monitor Punch and Die Wear
Regularly monitor the wear and condition of your punch and die components to ensure optimal performance and accuracy in metal punching operations. Inspect the cutting edges, surfaces, and profiles of your punches and dies for signs of wear, chipping, or deformation, and replace or resharpen worn tools as needed. Implement a preventive maintenance schedule to track tool usage and schedule maintenance tasks proactively to avoid unexpected downtime or quality issues.
Use Proper Tooling Setup
Proper tooling setup is critical for achieving consistent and repeatable results in metal punching operations. Ensure that your punch and die components are aligned correctly, securely mounted, and properly supported to minimize deflection, vibration, and tool deflection during the punching process. Use precision toolholders, fixtures, and clamping systems to maintain stability and accuracy throughout the punching operation.
Control Punch and Die Temperatures
Controlling punch and die temperatures is essential for preventing thermal damage and maintaining cutting performance in metalworking operations. Monitor the temperature of your punch and die components during punching processes and implement cooling strategies such as air blast systems, coolant sprays, or cryogenic cooling to dissipate heat and reduce thermal stress on the tools. Avoid prolonged exposure to high temperatures, which can lead to tool softening, wear, and premature failure.
Implement Proper Maintenance Practices
Implementing proper maintenance practices is essential for prolonging the lifespan and performance of a metal punch and die set. Develop a comprehensive maintenance schedule that includes regular inspection, cleaning, lubrication, and tool sharpening to keep your punch and die components in optimal condition. Train operators on proper tool handling and maintenance procedures to prevent misuse, mishandling, or damage to the tools.
Conclusion
Mastering the art of crafting the perfect metal punch and die setup requires careful planning, precision, and attention to detail. By following these ten expert tips, you can optimize your metalworking processes, improve cutting performance, and achieve high-quality results in your fabrication and manufacturing operations. Whether you're working with sheet metal, aluminum, or stainless steel, implementing these strategies will help you unlock the full potential of your punch and die sets and elevate your metalworking capabilities.
What's Your Reaction?
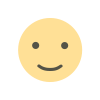
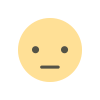
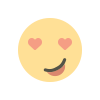
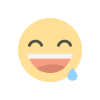
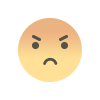
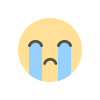
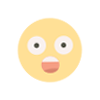